Kreislauf schafft Wert.
Der Geschäftsbereich WACKER SILICONES stellt ungefähr 3.000 verschiedene Siliconprodukte her. Dabei spielt die einzigartige Verbundproduktion am Standort Burghausen eine zentrale Rolle. Über Jahrzehnte wurden die Prozesse aufeinander abgestimmt und optimiert. Dadurch sind die Kosten für Rohstoffversorgung, Transport, Energie und Entsorgung deutlich gesunken. Das ausgefeilte System von Stoffkreisläufen ist damit einer der wichtigsten Hebel für die internationale Wettbewerbsfähigkeit des weltweit größten Standortes im Konzernverbund.
Wenn man sich einen Eindruck von der Verbundproduktion verschaffen will, beginnt man am besten mitten im Standort Burghausen bei der Siliciummahlung. Etwa 80 Prozent des Konzernumsatzes basieren auf Silicium. Der zweite wesentliche Verbundrohstoff Chlor wird nur wenige Meter entfernt in der Chlor-Alkali-Elektrolyse hergestellt. In Sichtweite befindet sich die Anlage zur Herstellung von pyrogener Kieselsäure (HDK®) und um zum Produktionskomplex für Siloxan zu kommen – der wichtigste Zwischenstoff für Silicone –, wechselt man nur auf die andere Seite des Alzkanals. „Die Verbundproduktion hier in Burghausen ist einzigartig in der Welt“, sagt Dr. Thomas Frey. „Die kurzen Wege und die eng miteinander verzahnten Kreisläufe versetzen uns in die Lage, den Einsatz von Rohstoffen und den Transport von Zwischenprodukten auf ein Minimum zu senken.“
Als Produktionsleiter Basics & Intermediates im Geschäftsbereich WACKER SILICONES ist der Verfahrenstechniker für die Herstellung von rund 250 Vorprodukten verantwortlich, die anschließend zu ungefähr 3.000 verschiedenen Siliconprodukten weiterverarbeitet werden. Silicone sorgen zum Beispiel dafür, dass Autos fahren, Flugzeuge fliegen oder Menschen schneller gesund werden. Ihre Anwendungsmöglichkeiten sind nahezu unbegrenzt.
Gute Karten im Wettbewerb
Dass WACKER etwa 60 Prozent seines Umsatzes außerhalb Europas erzielt und gleichzeitig über 80 Prozent seiner Produkte in Deutschland herstellt, ist dabei nur scheinbar ein Widerspruch. „Die Wettbewerbsfähigkeit eines Chemiestandortes entscheidet sich letztlich immer an der Frage, ob er in der Lage ist, Produkte in höchster Qualität zu geringsten Kosten herzustellen. Und da haben wir in Burghausen dank unseres ausgefeilten Verbundsystems trotz der im internationalen Vergleich hohen Kosten für Energie und Personal sehr gute Karten“, betont Dr. Rudolf Braun, der im Geschäftsbereich WACKER SILICONES die Einheit Basics & Intermediates leitet.
Produktionsleiter Thomas Frey unterquert auf seinem Rundgang einige der Leitungsbrücken, die sich rund fünf Meter über dem Erdboden auf einer Strecke von insgesamt 21 Kilometern durch das Werksgelände ziehen. Sie tragen dicke Bündel unterschiedlicher Rohre, die wie Adern die verschiedenen Anlagen miteinander verbinden. Einige dieser Leitungen versorgen die Betriebe mit Rohstoffen und Hilfsstoffen, andere transportieren die fertigen Produkte wieder ab. Dieses Rohrsystem bringt große Vorteile hinsichtlich der Kosten und der Sicherheit. Warum? „Weil wir beispielsweise für die Produktion jeder Tonne des wichtigsten Zwischenproduktes Siloxan ungefähr fünf Tonnen chlorhaltiger, also ätzender Flüssigkeiten und Gase bewegen, die mehrere Produktionsschritte und damit mehrere Anlagen durchlaufen müssen“, sagt Frey. „Das ist nur mit Hilfe dieser Rohrleitungssysteme möglich.“
Handfeste Erfolge
Siliconprodukte werden hier in Ostbayern seit den 1950er Jahren hergestellt. Seitdem haben die Ingenieure und Chemiker die chemischen Prozesse nicht nur stetig verbessert, sondern auch immer enger miteinander verzahnt – mit handfesten Erfolgen bei der Produktionsmenge, den Energiekosten und der Rohstoffausbeute. So konnte zum Beispiel der spezifische Energiebedarf der Siloxanproduktion in den letzten fünf Jahren um etwa ein Drittel gesenkt werden.
Spitzenwerte erreicht die Verbundproduktion auch bei der Rohstoffausbeute. Im Werk Burghausen stellt WACKER nicht nur Silicone her, sondern auch kristallines Silicium, das später in Solarzellen und Computerchips zum Einsatz kommt. Da beide Produktionslinien auf Siliciummetall als Ausgangsstoff aufbauen, mahlt die Siliciummahlung das angelieferte Material in unterschiedliche Korngrößen, je nach Bedarf. „Wir können auf diese Weise praktisch 100 Prozent des Rohstoffes verwerten“, sagt Frey. „Das wäre bei nur einer Produktlinie gar nicht oder nur mit immensem Aufwand möglich.“
Den aus Chlor hergestellten Chlorwasserstoff (HCl) wiederum fährt WACKER in einem weitgehend geschlossenen Kreislauf. Da HCl-Moleküle bei der Herstellung von Siliconen und Polysilicium fast nur als Hilfsstoff benötigt werden, lassen sie sich mit einem gewissen Aufwand ohne Qualitätsverluste zurück in den Produktionsprozess koppeln. Dieses Recycling wurde bis heute so optimiert, dass jedes Chloratom den Kreislauf statistisch acht Mal durchläuft, bevor es das Werk als Zwischenprodukt oder als chemisch gebundener Reststoff in Form von Kochsalz (NaCl) verlässt. Die Folge: Am Standort wird heute ein Viertel weniger frisches HCl benötigt als noch vor ein paar Jahren. Im gleichen Zeitraum haben aber die Geschäftsbereiche ihre Produktionsmengen deutlich gesteigert.
Eine entscheidende Rolle im Produktionsverbund spielt die Anlage für pyrogene Kieselsäure (HDK®). „Bei der Herstellung von Polysilicium fällt als Nebenprodukt Tetrachlorsilan in großen Mengen an. Das kann entweder direkt in den Produktionsprozess zurückgeführt werden oder wir verarbeiten es weiter zu pyrogener Kieselsäure. Außerdem sind wir mittlerweile in der Lage, auch Nebenprodukte aus der Siliconproduktion als Rohstoff bei der HDK®-Herstellung einzusetzen, die ansonsten entsorgt werden müssten. Das im Prozess frei werdende HCl geht zurück in den Verbundkreislauf“, erläutert Produktionsleiter Frey. Mit HDK® veredelt WACKER nicht nur seine eigenen Silicone, sondern verkauft es auch an externe Kunden, die es beispielsweise als Füllstoff in Isolierpaneelen oder in Klebstoffen verwenden. Die HDK®-Anlage schlägt damit drei Fliegen mit einer Klappe: Sie erhöht die Wertschöpfung am Standort, sie reduziert die Abfälle und dient dem HCl-Recycling.
WACKER-Verbundproduktion ist die Basis für hohe Kosten-, Energie- und Ressourceneffizienz
In hochkomplexen Stoff- und Energiekreisläufen werden Nebenprodukte und Abwärme in die Produktion zurückgeführt und für die weitere Wertschöpfung genutzt.
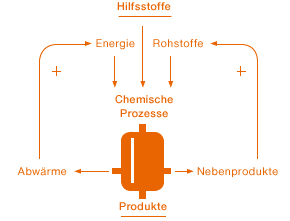
Exportschlager Verbundkompetenz
Seine Verbundkompetenz exportiert das Werk Burghausen auch an andere Standorte. So wurde die Siloxankapazität im sächsischen Nünchritz seit dem Kauf des Werks im Jahr 1998 auf rund 130.000 Tonnen erweitert, sieben Mal so viel wie bei der Übernahme. Das übertrifft sogar die aktuelle Produktion in Burghausen. In China ist WACKER inzwischen ebenfalls mit einem Großstandort für die Siliconherstellung präsent, weitere Werke sollen folgen. „Unser Ziel ist es, weltweit integrierte Standorte zu schaffen“, blickt Rudolf Braun nach vorn.
Aber auch in Europa werden die Kapazitäten weiter steigen. Der Markt für Silicone wächst mengenmäßig jährlich um rund sechs Prozent. Dieses Tempo müssen die Werke in Burghausen und Nünchritz halten. Dazu werden in beiden Werken systematisch alle chemischen, verfahrenstechnischen und logistischen Prozesse auf den Prüfstand gestellt und Produktionsengpässe beseitigt. „Ziel ist es“, sagt Braun, „dadurch unsere Siloxanproduktion in den kommenden fünf Jahren um jeweils 10.000 Tonnen zu steigern.“ Die Optimierung der Verbundproduktion an den Standorten in Europa, da ist sich der Chemiker sicher, ist noch längst nicht ausgereizt.