Auf in die Zukunft – die Themen von morgen gestalten
3D-Druck
Der Andrang war riesengroß. Auf der 20. internationalen Messe für Kunststoff und Kautschuk K 2016 wollten viele Fachbesucher den ersten industriellen 3D-Drucker für Silicon sehen. WACKER präsentierte damit eine echte Weltneuheit. Nicht weniger innovativ ist das Geschäftsmodell. Kunden können ihr Design im Webshop hochladen oder im Open Print Lab unter fachlicher Anleitung selbst drucken. Das Produkt erhalten sie anschließend zugeschickt.
Bis 2021, so das unabhängige US-Beratungsinstitut Wohlers Associates, werden mit 3D-Verfahren mehr als 26 Milliarden US-Dollar umgesetzt.
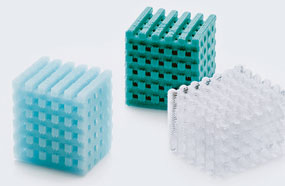
Die WACKER-Technologie beruht auf dem Drop-on-Demand-Verfahren: Der Drucker deponiert winzige Silicontröpfchen auf einer Unterlage, die innerhalb kürzester Zeit eine homogene Schicht aus Silicon bilden.
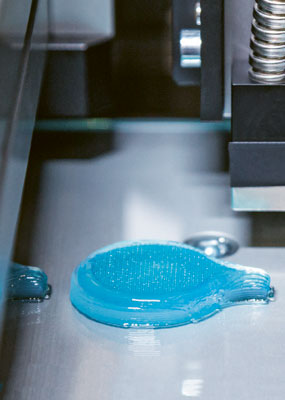
Anschließend beginnt der Druckvorgang von neuem. So entstehen, Schicht für Schicht, Bauteile in den verschiedensten Formen, Farben und Härtegraden – der Phantasie sind keine Grenzen gesetzt. Mit Stützmaterial lassen sich sogar Überhänge, Gitterstrukturen und komplexe Geometrien drucken.
WACKER vermarktet das neue 3D-Verfahren unter dem Namen ACEO®. Es bietet ganz neue Produktions- und Gestaltungsmöglichkeiten. Prototypen aus Silicon lassen sich jetzt schnell und ohne großen technischen Aufwand drucken – eine Computerzeichnung oder ein mittels bildgebenden Verfahrens hergestelltes Abbild genügt. Sogar Ersatzteilhersteller profitieren von der neuen WACKER-Technik: Dichtungen oder andere Teile aus Silicon müssen jetzt nicht mehr aus Kostengründen in großen Serien produziert werden. Bei Bedarf wird einfach nachgedruckt. Sogar webbasierte Wertschöpfungsketten sind möglich – Industrie 4.0 lässt grüßen. Großkonzerne aus der Auto-, Luft- und Raumfahrtindustrie interessieren sich ebenso für das innovative 3D-Verfahren wie Hersteller aus der Sport-, Freizeit- und Life-Science-Industrie. Die Vision, Silicone mit einem industrietauglichen Verfahren dreidimensional zu drucken, ist jetzt Realität.
Wellenkraftwerk

Wenn die Wellen gegen die Kaimauer branden und die Gischt haushoch spritzt, bekommen auch Landratten eine Ahnung von den gewaltigen Energien, die hier freigesetzt werden. Nach einer Hochrechnung der Vereinten Nationen speichern Wellen ein Energiepotenzial von 29.500 Terawattstunden – mehr, als die gesamte Menschheit im Jahr an Energie benötigt. Bislang gibt es aber kein technisch ausgereiftes System, um diese Kraft zuverlässig und kostengünstig zu „ernten“. Mechanische oder hydraulische Kraftwerke sind dafür denkbar ungeeignet. Sie müssen auf hoher See ständig gewartet werden.
Wellen speichern ein Energiepotenzial von 29.500 TWh.
Die Industrie geht deshalb neue Wege. Die Lösung: wassergefüllte Gummischläuche, die mit flexiblen Kondensatoren aus elektroaktiven Materialien bestückt sind. Durch das Auf und Ab der Wellen werden die Minikraftwerke ständig gedehnt und gepresst. Dabei wandeln sie die mechanische Energie der Welle in elektrischen Strom um. Die Schläuche sind wartungsfrei und extrem effizient.
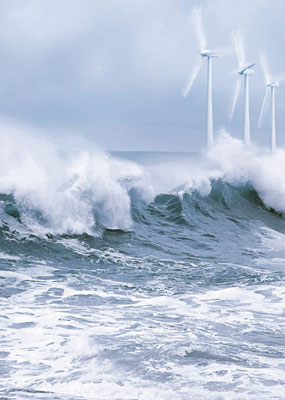
WACKER liefert das wichtigste Ausgangsmaterial für den Konverter: hauchdünne Folien aus Silicon. Nur sie besitzen die richtigen elektrischen Eigenschaften. Außerdem sind sie extrem flexibel und wartungsfrei.
WACKER ist das einzige Unternehmen auf der Welt, das die Präzisionsfolien in größeren Stückzahlen herstellt. Die ersten Prototypen mit dem WACKER-Material werden bereits getestet. In wenigen Jahren könnten schon die ersten Kraftwerke einsatzbereit sein. Mit Wellenkonvertern aus Silicon ließe sich dann vor den Küsten der Welt mittels der nie versiegenden Auf- und Abwärtsbewegung der Wellen Strom erzeugen.
Jeder Spitzensportler weiß es: Höchstleistungen erreicht man nur, wenn man niemals damit aufhört, an sich zu arbeiten, um immer noch besser zu werden. Wer sich dieser Daueraufgabe nicht stellt, der fällt zurück.
120 Prozessoren, 8 Millionen Punkte, 10s Echtzeit benötigen 3 Wochen Rechenzeit
Bei WACKER ist das nicht anders. Schon vor fünf Jahrzehnten begann das Unternehmen mit der Herstellung pyrogener Kieselsäure. Das farblose Pulver – Siliciumdioxid in hochreiner, amorpher Form – steckt in vielen Alltagsprodukten.
Es isoliert Kühlschränke, steuert die Fließfähigkeit von Lacken und Klebstoffen, verhindert, dass Tonerpulver klumpt, und macht Silicone fest wie Gummi.
Heute ist WACKER weltweit die Nummer drei in diesem Geschäft. Und die Nachfrage nach HDK®, wie das Produkt bei WACKER heißt, steigt weiter. Chemiker und Ingenieure in Burghausen entwickeln deshalb den perfekten Reaktor. Ziel ist es, die Ausbeute zu steigern, HDK® in noch besserer Qualität herzustellen und die Herstellkosten deutlich zu minimieren.
Pyrogene Kieselsäure entsteht in einer Knallgasflamme bei über 1.000 °C. Um zu verstehen, was dabei passiert, simulierten WACKER-Forscher den Prozess am Computer. 120 Prozessoren müssen jedes Mal über acht Millionen Punkte berechnen. Zehn Sekunden Echtzeit benötigen eine Rechenzeit von bis zu drei Wochen. Die Hochleistungscomputer arbeiten dabei rund um die Uhr.
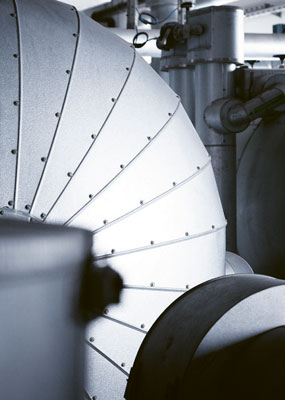
Doch der Aufwand hat sich gelohnt. Mit den Berechnungen konnte WACKER einen Pilotreaktor in Burghausen bauen. Dort werden jetzt Versuche durchgeführt, von denen alle HDK®-Anlagen von WACKER profitieren werden – auch die neue Produktion in Charleston, USA.
F & E

Wie kommt das Neue in die Welt? Es ist ein Mix aus Wissen, Kreativität und Ausdauer. Und dem Willen, die Dinge besser zu machen. Im Geschäftsbereich WACKER SILICONES arbeiten mehr als 400 Mitarbeiter an den Produkten von morgen. Das sind rund zehn Prozent der Mitarbeiter in diesem Bereich. Dank ihrer besonderen chemischen und mechanischen Eigenschaften sind die Anwendungsmöglichkeiten von Siliconen so vielfältig wie bei kaum einem anderen Werkstoff und eine wichtige Quelle für unser künftiges Wachstum. Derzeit laufen über 100 Forschungsprojekte bei WACKER SILICONES. Und das zahlt sich aus. Die Neuproduktrate, also der Umsatz mit Produkten, die jünger sind als fünf Jahre, wächst dreimal schneller als das Geschäft mit Silicontypen, die schon länger am Markt sind.
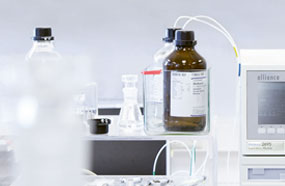
2017
Ann Arbor
Ein weiterer Erfolgsfaktor ist die Internationalisierung der Forschungs- und Entwicklungsarbeit. Unser Drei-Stufen-Modell besteht aus technischen Kompetenzzentren, der WACKER-Academy und internationalen Forschungsstätten. Unser neues Labor in Ann Arbor im US-Bundesstaat Michigan ist das jüngste Baby in unserem weltweiten Forschungsnetzwerk für Silicone. Ab Mitte 2017 entwickeln wir dort innovative Produkte für die Märkte in Nord-, Mittel- und Südamerika. Dazu zählen Anwendungen und Lösungen für die Gesundheits-, Medizin-, Elektronik-, Life-Science- und Beschichtungsindustrie. Der 1.000 Quadratmeter große Laborkomplex mit eigener Analytik residiert unweit der University of Michigan, einer der renommiertesten Universitäten der USA. Die Mischung aus Wissenschaft, zahlreichen Startups und erfolgreich etablierten Unternehmen ist genau die Atmosphäre, die nötig ist, um neue Anwendungen und Produkte zu entwickeln. Das Ziel ist klar: WACKER will auf dem zweitgrößten Chemiemarkt der Welt weiter wachsen.
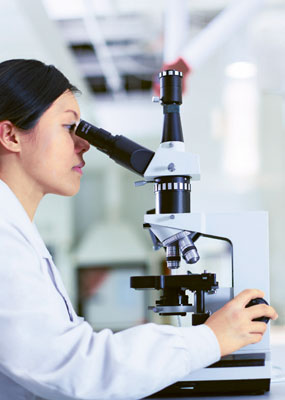
Siliciuminstitut von WACKER an der Technischen Universität München

WACKER zapft auch das Wissen externer Experten und Wissenschaftler an. Deshalb haben wir mit der deutschen Exzellenzuniversität TU München vor mehr als zehn Jahren das Institut für Siliciumchemie ins Leben gerufen, das weltweit einzigartig ist. Die Siliciumchemie ist ein noch junges Arbeitsgebiet, deren Potenzial noch längst nicht ausgeschöpft ist. Wesentliche Zukunftsthemen wie die Informationstechnologie, die regenerative Energieerzeugung oder die Elektromobilität sind ohne Siliciumchemie nicht zu verwirklichen. Unser Ziel ist es, die neuesten Forschungsergebnisse mit der Erfahrung und dem Wissen von WACKER aus 70 Jahren auf dem Gebiet der Siliconforschung zu verbinden. Die ersten Ergebnisse aus dieser Verbindung von Wissenschaft und Wirtschaft können sich sehen lassen: über 30 Forschungsprojekte, zehn neue Patente und 35 wissenschaftliche Publikationen.
Um die Siliciumchemie weiter voranzubringen, neuen Forschungsansätzen auf die Sprünge zu verhelfen und Produktinnovationen möglich zu machen, ist WACKER schon vor 30 Jahren neue Wege gegangen. Wir haben den WACKER Silicone Award kreiert. Damit fördern wir herausragende Forschungsarbeiten auf dem Gebiet der siliciumorganischen Chemie. Er zählt zu den bedeutendsten internationalen Auszeichnungen auf diesem Sektor. Bisher haben 19 internationale Forscher den Siliconpreis erhalten. Der jüngste Preisträger ist Professor Dr. Alexander Filippou, Siliciumforscher an der Rheinischen Friedrich-Wilhelms-Universität Bonn, der den Preis im September 2016 bei den europäischen Silicontagen in Posen entgegennehmen konnte.