Defossilization
Renewable Substances for Chemical Processes
Carbon, hydrogen and methanol are important base materials in chemistry. We need them to be able to manufacture silicon and silicones. WACKER is looking for alternatives to fossil fuels for its processes. Charcoal instead of coal. Green hydrogen instead of gray hydrogen. At the same time, CO2 must become a raw material rather than a waste product.
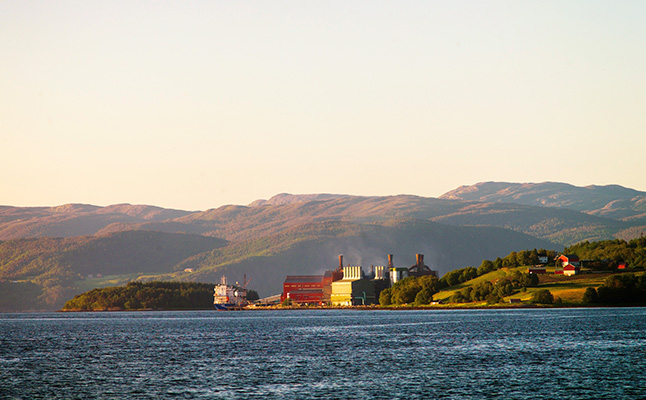
Coal and charcoal hardly differ in terms of appearance: both are black with a shiny, silvery surface. But in terms of how they were formed, they couldn’t be more different. Coal formed over millions of years when, deep below the earth’s surface, under high pressure and temperature, plant residues turned into coal. Therefore, it is a fossil fuel. However, charcoal is produced when wood is heated at high temperature with a lack of oxygen. This makes it a renewable fuel.
“We want to replace coal with charcoal in the production of silicon. In this way, we aim to save as much as 430,000 metric tons of CO2 a year.”
Silicon Metal for Silicones and Polysilicon
Coal is an important raw material in the production of silicon metal – which is the case at WACKER, too. At its plant in Holla, Norway, the company produces approximately 70,000 metric tons of silicon metal a year – accounting for 25 to 30 percent of the Group’s annual requirements. The raw material is transported from Holla to Burghausen and Nünchritz, where silicones and polysilicon are made from silicon metal for the solar and semiconductor industries.
The manufacturing process in Holla involves a reduction process, in which quartz (silicon dioxide) is reduced with coal in electric arc furnaces at 2,000 degrees Celsius. This is how the oxygen is removed from the silicon dioxide. The result is metallurgical-grade silicon. Coal, which used to bring the quartz to a red-hot glow, is now to be replaced by charcoal or other plant-based compounds. “Our aim is to thereby save up to 430,000 metric tons of CO2 per year,” says Silje Gridsvåg, who heads WACKER’s Holla Charcoal project. 430,000 tons – that’s the amount of CO2 emitted if some 800,000 cars drove from Burghausen (Bavaria, Germany) to Holla (Norway) and back, a distance of 2,250 kilometers one way (including the ferry).
The Holla project is currently in the validation phase. Silje Gridsvåg is sounding out different technologies in discussion with possible partners. Whether the charcoal will be purchased or whether WACKER will produce the charcoal itself in the future has yet to be decided. What is certain is that the wood will come from sustainable forests.
The next step is to get a pilot facility up and running in Holla. Initially, the idea is to save several thousand metric tons of charcoal per year. “After that, we want to upscale the process,” says Gridsvåg. The aim is to gradually replace coal with charcoal. Once the entire production setup has been switched over, 430,000 metric tons of CO2 a year will be saved.
“Using biomass is deemed to be carbon neutral as only the carbon dioxide that the plants have utilized is released during combustion,” she explains. CO2 emissions cannot be completely avoided during the production of silicon. “We talk about ‘unavoidable’ emissions as there is no other relevant production process,” says Gridsvåg. “However, unavoidable does not mean that the CO2 cannot be used.”
“Producing one metric ton of hydrogen generates approximately 10 metric tons of CO2, whereas green hydrogen is carbon-neutral. The production of green methanol does not involve any CO2 either.”
CO2: From Waste Product to Raw Material
At the moment, the CO2 generated in processes, such as silicon production in Holla, is a waste product that is emitted into the atmosphere. WACKER aims to change that. “We have several ideas about how to use CO2 as a raw material in the future,” says Peter Gigler. He is in charge of another WACKER project aimed at defossilizing production, known as RHYME Bavaria. The acronym RHYME stands for Renewable Hydrogen and Methanol. The project is to be implemented at WACKER’s Burghausen site in Bavaria, hence the name RHYME Bavaria.
WACKER wants to build a 20-megawatt electrolysis plant in Burghausen to generate hydrogen using electricity from renewable sources. The next step will be to convert this hydrogen into methanol in a synthesis plant using CO2 from existing processes. “This is how to turn the waste product CO2 into a value-added raw material,” says Gigler. Around 20,000 metric tons of CO2 are to be saved as a result. “What’s more, unlike the conventional synthesis of hydrogen and methanol, the new methods will cut CO2 emissions by as much as 100 percent.”
RHYME Bavaria
Production Processes Based on Green Hydrogen Might Look Like This:
Up until now, conventional hydrogen has been used in production processes at WACKER. This is also known as gray hydrogen, gray meaning that this hydrogen has been obtained from fossil fuels. Usually, it is natural gas which is converted under heat into hydrogen and CO2. This is a proven process which does, however, have an adverse effect on the environment. “Producing one metric ton of hydrogen generates approximately 10 metric tons of CO2, whereas green hydrogen is carbon-neutral. The production of green methanol does not involve any CO2 either,” he says.
Both hydrogen and methanol are important starting materials for a wide range of chemical products. Silicones for medical products, polymer fibers for the textile industry, ultrapure silicon for photovoltaic applications, plastics for packaging, adhesives, paints and much more. “Green hydrogen and renewable methanol have the potential to defossilize industry,” says Gigler. “With RHYME Bavaria we want to show that this is technically feasible.”
Producing renewable hydrogen and methanol is not yet economically viable. “We need large quantities of renewable energy at affordable prices,” he says, adding that, to be cost-effective, the limit had to be 4 cents per kilowatt-hour. WACKER has applied for funding for RHYME Bavaria. If the funding application is approved, the facilities could go on stream by late 2025.